Efficient warehouse inventory management is critical for businesses aiming to meet customer demands, optimize operations, and maintain profitability. Warehouse inventory refers to the goods and materials that are stored in a warehouse, waiting to be sold, distributed, or used in manufacturing processes. Managing this inventory involves tracking, organizing, and maintaining the right quantities of products while ensuring minimal waste and cost.
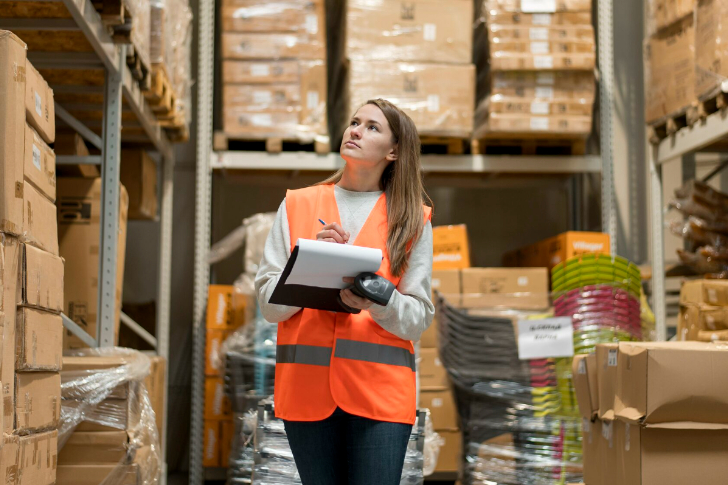
Effective inventory management improves operational efficiency, reduces costs, and enhances customer satisfaction by ensuring that products are available when needed.
This article explores the importance of warehouse inventory management, strategies for effective management, and best practices that can help businesses streamline their operations. Additionally, it discusses the role of technology and automation in improving accuracy and reducing errors in inventory control.
The Importance of Warehouse Inventory Management
Warehouse inventory management plays a significant role in overall supply chain efficiency. Here are some of the key reasons why it is essential:
1. Meeting Customer Demands
A well-managed inventory ensures that businesses can meet customer demands promptly. Stockouts (when a product is unavailable) or overstocking (having excessive quantities of products) can lead to lost sales or unnecessary holding costs. Accurate inventory management helps strike the right balance, ensuring that products are available when needed without tying up unnecessary capital.
2. Cost Reduction
Effective inventory management helps businesses avoid the costs associated with overstocking, such as storage fees, insurance, and the risk of inventory obsolescence. On the other hand, understocking can lead to expedited shipping costs, lost revenue, and customer dissatisfaction. By managing inventory levels carefully, businesses can reduce operational costs and increase profitability.
3. Improving Operational Efficiency
Properly organized inventory allows warehouses to function smoothly. Inventory management systems (IMS) help track stock levels, item location, and movement, enabling warehouse staff to pick, pack, and ship products quickly and accurately. This reduces errors and delays, ultimately improving overall productivity.
4. Enhanced Data Accuracy
Manual inventory management can be error-prone. Using automated systems or technologies such as barcode scanning and RFID tracking ensures that inventory data is accurate and up-to-date. This helps warehouse managers make informed decisions regarding stock levels, reordering schedules, and product placement.
5. Inventory Visibility
An organized and transparent inventory system provides real-time visibility of stock levels, which is crucial for decision-making. Managers can easily monitor stock movement, track sales trends, and anticipate future inventory needs.
Key Components of Warehouse Inventory Management
1. Inventory Types
Warehouses store different types of inventory, and understanding each type is essential for managing them effectively. The primary types of warehouse inventory include:
- Raw Materials: These are the components used in the production of finished goods.
- Work-in-Progress (WIP): Items that are in the process of being manufactured but are not yet complete.
- Finished Goods: Products that are ready for sale or distribution.
- MRO (Maintenance, Repair, and Overhaul) Inventory: Supplies used for the maintenance and repair of equipment and machinery.
2. Inventory Storage Systems
Effective storage systems are crucial for managing inventory efficiently. Some of the most common warehouse storage systems include:
- Racking Systems: These are structures used to store items vertically, which helps maximize space.
- Shelving Units: These are ideal for smaller items and can be used for organizing products of various sizes.
- Bins and Containers: Smaller bins or boxes are useful for categorizing small parts or products.
3. Inventory Tracking and Movement
Tracking inventory movement involves monitoring the flow of goods in and out of the warehouse. Inventory tracking can be done through:
- Barcode Scanning: A common and cost-effective method for tracking products.
- Radio Frequency Identification (RFID): A more advanced tracking system that uses radio waves to identify products.
- Manual Counts: In some cases, especially in smaller warehouses, manual counting of stock may still be used, though it is prone to human error.
4. Reordering and Restocking
One of the most critical aspects of inventory management is knowing when to reorder products. Stock levels need to be monitored continuously to avoid shortages. The use of automated reordering systems helps maintain optimal stock levels.
Strategies for Effective Warehouse Inventory Management
1. ABC Analysis
The ABC analysis technique categorizes inventory into three groups (A, B, and C) based on their importance and value to the business:
- A Items: High-value items with low sales frequency. These require tight control and regular monitoring.
- B Items: Moderate-value items with moderate sales frequency. These require periodic checks.
- C Items: Low-value items with high sales frequency. These are less critical but should still be tracked.
By implementing the ABC analysis, warehouses can focus their resources on the most critical items, ensuring they are always in stock while minimizing excess inventory for less critical items.
2. Just-In-Time (JIT) Inventory Management
JIT inventory management is a strategy where inventory is ordered and delivered just in time to meet production or customer demand. This minimizes the need for large inventories, reduces storage costs, and lowers the risk of obsolescence. However, it requires precise forecasting and strong relationships with suppliers.
3. Cycle Counting
Cycle counting is a practice where a portion of the inventory is counted regularly, instead of performing a full physical inventory count. This helps reduce the time and cost associated with full counts and allows for continuous monitoring of inventory accuracy.
4. Warehouse Layout Optimization
The physical layout of the warehouse affects how efficiently inventory is managed. A well-designed warehouse layout should minimize travel time for workers, reduce handling costs, and make it easy to locate and retrieve items.
5. Automation and Technology
Technology has revolutionized inventory management. Automated systems, such as Warehouse Management Systems (WMS), can track inventory in real-time, update stock levels instantly, and even automate reorder processes. Technologies like drones and robots are also increasingly being used to speed up inventory counting and improve accuracy.
Best Practices for Warehouse Inventory Management
1. Implement a Robust Inventory Management System
A reliable and scalable inventory management system (IMS) is the backbone of an efficient warehouse. WMS can offer functionalities such as real-time stock tracking, barcoding, reporting, and integration with other business systems like Enterprise Resource Planning (ERP) software.
2. Regularly Review and Update Inventory Policies
Inventory management policies should be periodically reviewed to ensure they are aligned with business goals, market conditions, and technological advancements. Policies should cover areas like reorder points, stock level thresholds, and the handling of excess or obsolete inventory.
3. Staff Training and Development
Warehouse staff should be trained in proper inventory management techniques, the use of tracking technologies, and safety procedures. Regular training ensures that workers are familiar with best practices, which reduces errors and enhances overall efficiency.
4. Establish Strong Supplier Relationships
Strong relationships with suppliers are crucial for maintaining stock levels and ensuring timely deliveries. A reliable supply chain ensures that inventory shortages are minimized and that products are consistently available when needed.
Table 1: ABC Inventory Analysis
Category | Value | Frequency of Use | Inventory Control Strategy |
---|---|---|---|
A Items | High | Low | Tight control, frequent monitoring, and reorder strategy |
B Items | Moderate | Moderate | Periodic checks and reordering as needed |
C Items | Low | High | Minimal control, bulk ordering and occasional checks |
Table 2: Benefits of Automation in Warehouse Inventory Management
Technology | Benefit |
---|---|
Barcode Scanning | Faster product identification and tracking |
RFID Technology | Real-time stock visibility and enhanced accuracy |
Automated Replenishment | Reduces stockouts and overstocking by automating the reorder process |
Drones and Robots | Improves stock counting speed and reduces errors |