In the intricate dance of modern supply chains, the warehouse stands as a critical intermediary, a dynamic hub where goods are received, stored, and dispatched to meet ever-increasing customer demands. Effective warehouse management transcends mere storage; it encompasses a complex web of processes, from optimizing space utilization and ensuring inventory accuracy to streamlining order fulfillment and managing labor efficiently. In today’s fast-paced and competitive environment, relying on manual processes is no longer sustainable.
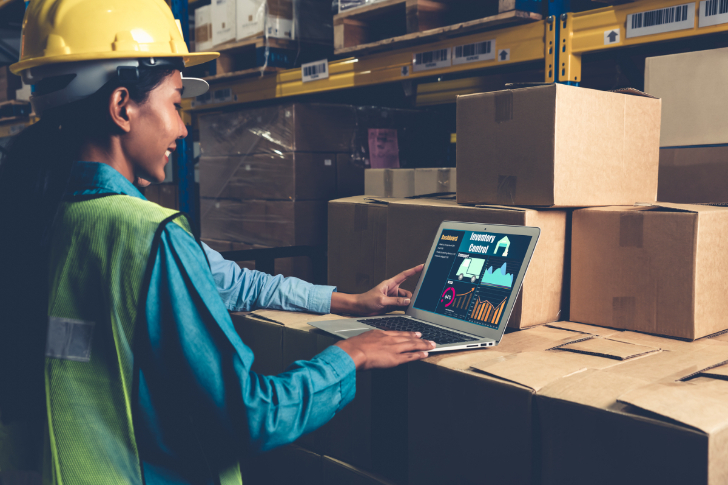
This is where Warehouse Management Systems (WMS) emerge as indispensable tools, offering sophisticated capabilities to orchestrate warehouse operations and drive significant improvements in efficiency, cost-effectiveness, and overall supply chain performance.
Warehouse management is the art and science of controlling the movement and storage of materials within a warehouse and processing the associated transactions, including shipping, receiving, put-away, and picking. Its primary goal is to maximize the efficiency of these operations while minimizing costs and ensuring the timely and accurate fulfillment of orders. A well-managed warehouse acts as a strategic asset, contributing directly to a company’s bottom line and its ability to meet customer expectations. Conversely, a poorly managed warehouse can lead to a cascade of problems, including lost inventory, shipping errors, delays, increased labor costs, and ultimately, dissatisfied customers.
The Symphony of Efficiency: Key Processes in Warehouse Management
Effective warehouse management hinges on the seamless execution of several interconnected processes:
- Receiving: This initial stage involves accepting incoming goods, verifying them against purchase orders, inspecting for damage or discrepancies, and updating inventory records. Accuracy and speed in receiving are crucial to prevent delays and ensure the integrity of the incoming stock.
- Put-Away: Once received, goods need to be strategically placed in designated storage locations within the warehouse. Efficient put-away considers factors like product type, size, weight, frequency of picking, and storage space optimization to minimize travel time and maximize space utilization.
- Storage: Proper storage techniques are essential to maintain the quality and accessibility of inventory. This includes determining optimal storage layouts, utilizing appropriate racking and shelving systems, and implementing environmental controls when necessary (e.g., temperature-controlled storage for perishable goods).
- Picking: This is the process of retrieving specific items from their storage locations to fulfill customer orders. Various picking methods exist, including zone picking, batch picking, and wave picking, each with its own advantages depending on the order volume and warehouse layout. Accuracy and speed are paramount in this labor-intensive process.
- Packing: Once picked, items need to be securely and efficiently packed for shipment. This involves selecting appropriate packaging materials, ensuring proper labeling, and potentially including packing slips or other documentation.
- Shipping: The final stage involves selecting the appropriate carrier, generating shipping labels, loading the packed goods onto transport vehicles, and updating order status information. Timely and accurate shipping is critical for customer satisfaction.
- Inventory Control: Maintaining accurate records of inventory levels and locations is fundamental to effective warehouse management. This involves regular cycle counts, physical inventory audits, and the reconciliation of discrepancies to ensure data integrity and prevent stockouts or overstocking.
- Returns Management (Reverse Logistics): Handling returned goods efficiently is an increasingly important aspect of warehouse management. This includes receiving returned items, inspecting their condition, determining the reason for return, and processing refunds, replacements, or restocking.
The Digital Revolution: The Power of Warehouse Management Systems (WMS)
Modern warehouse operations are increasingly reliant on Warehouse Management Systems (WMS) – sophisticated software solutions designed to manage and optimize the entire spectrum of warehouse processes. A WMS provides real-time visibility into inventory, automates tasks, improves accuracy, and empowers warehouse managers to make data-driven decisions. The benefits of implementing a WMS are manifold:
- Enhanced Inventory Accuracy: Real-time tracking and automated data capture significantly reduce errors associated with manual record-keeping, leading to more accurate inventory counts and reduced discrepancies.
- Improved Operational Efficiency: Automation of tasks like picking routes, put-away suggestions, and shipping label generation streamlines workflows, reduces travel time, and increases overall productivity.
- Optimized Space Utilization: WMS can analyze storage patterns and recommend optimal placement strategies, maximizing the use of available warehouse space and potentially delaying the need for expansion.
- Reduced Labor Costs: By automating tasks and optimizing workflows, a WMS can help businesses manage with a more efficient workforce, reducing the need for excessive manual labor.
- Better Order Fulfillment: Accurate inventory data and streamlined picking and packing processes lead to faster and more accurate order fulfillment, enhancing customer satisfaction and reducing shipping errors.
- Real-Time Visibility and Reporting: WMS provides comprehensive reports and real-time dashboards on key performance indicators (KPIs) such as inventory levels, order cycle times, and labor productivity, enabling managers to identify bottlenecks and areas for improvement.
- Improved Decision-Making: Access to accurate and timely data empowers warehouse managers to make informed decisions regarding purchasing, staffing, and operational strategies.
- Seamless Integration: Many WMS solutions can integrate with other crucial business systems, such as Enterprise Resource Planning (ERP), Transportation Management Systems (TMS), and e-commerce platforms, creating a unified flow of information across the supply chain.
Navigating the Landscape: Key Features of a Modern WMS
A robust WMS typically encompasses a wide array of features designed to address the complexities of modern warehouse operations:
- Inventory Tracking and Visibility: Real-time tracking of inventory levels, location, and status across multiple warehouses.
- Receiving and Put-Away Management: Streamlined receiving processes, guided put-away tasks based on predefined rules, and cross-docking capabilities.
- Order Management and Picking: Support for various picking strategies (e.g., zone, batch, wave), pick-to-light or pick-by-voice integration, and route optimization.
- Packing and Shipping: Automated packing instructions, shipping label generation, and integration with various shipping carriers.
- Yard Management: Management of inbound and outbound truck schedules and dock door assignments.
- Labor Management: Tracking employee performance, assigning tasks, and optimizing labor utilization.
- Reporting and Analytics: Customizable reports and dashboards on key warehouse metrics.
- Integration Capabilities: APIs and connectors for seamless integration with other business systems.
- Mobile Capabilities: Support for handheld devices and mobile applications for real-time data capture and task management.
- Warehouse Layout Optimization: Tools to analyze and optimize warehouse layout for efficient flow and space utilization.
The Investment in Efficiency: Understanding WMS Costs
The cost of implementing a WMS can vary significantly depending on factors such as the size and complexity of the warehouse operation, the chosen software vendor, the deployment model (cloud-based vs. on-premise), the number of users, and the level of customization required.
Table 1: Estimated Cost Ranges for Cloud-Based WMS for Different Warehouse Sizes
Warehouse Size | Number of Users | Typical Monthly Subscription Cost (£) | Key Features Typically Included | Suitable For |
---|---|---|---|---|
Small (1-5 users) | 1-5 | £200 – £800 | Basic inventory tracking, order management, shipping integration, basic reporting. | Startups, small e-commerce businesses, single-warehouse operations. |
Medium (6-20 users) | 6-20 | £800 – £2,500 | Advanced inventory management (batch/serial tracking), multi-location support, enhanced reporting, integration with accounting/e-commerce platforms. | Growing SMEs, businesses with multiple sales channels, and more complex inventory needs. |
Large (21+ users) | 21+ | £2,500+ (Custom Pricing) | Highly customizable features, advanced analytics and forecasting, labor management, yard management, extensive integration capabilities. | Large enterprises, businesses with complex supply chains, multiple warehouses, and high transaction volumes. |
Note: These are estimated monthly costs for cloud-based WMS solutions. On-premise solutions will have different pricing structures involving upfront license fees and ongoing maintenance costs.
Table 2: Key Factors Influencing WMS Implementation Costs
Factor | Description | Impact on Cost |
---|---|---|
Software Vendor & Tier | Different vendors offer varying features and pricing models. Higher-tier plans with more advanced functionality will cost more. | Higher-end vendors and more comprehensive plans lead to increased costs. |
Deployment Model | Cloud-based (SaaS) vs. on-premise deployment. | Cloud-based typically involves lower upfront costs but recurring subscription fees. On-premise requires higher initial investment in licenses and infrastructure. |
Number of Users | Most WMS solutions are priced per user per month. | More users directly translate to higher subscription or license costs. |
Integration Complexity | The number and complexity of integrations with other business systems (ERP, TMS, e-commerce platforms). | More complex integrations require more development effort and can increase implementation costs. |
Customization Requirements | The extent to which the WMS needs to be tailored to specific business processes and workflows. | Significant customization will increase implementation time and costs. |
Training and Support | The cost of training staff on the new system and ongoing technical support. | Comprehensive training programs and premium support packages will add to the overall cost. |
Data Migration | The effort involved in transferring existing data from legacy systems to the new WMS. | Complex data migration can be time-consuming and costly. |